In the aerospace industry, every ounce of weight contributes to the amount of fuel needed to keep airborne. For a commercial airliner, the cost of fuel is well over half of the total running costs. Over the full lifetime of a plane, even the smallest component represents thousands of US dollars of operational expenditure. Along with the financial cost, there is an environmental cost to consider, which is also directly related to the total weight.
Optimizing Energy Efficiency in Powered Flight
By definition, powered flight will always require energy, but the amount of energy needed is related to the overall weight of the aircraft. It follows that aerospace companies are keen to explore new technologies that can limit that weight, lower operational costs, and help reduce the subsequent emissions.
This may involve using lighter alloys where structurally possible. Around 80% of an aircraft’s unloaded weight is attributable to aluminum alloy, while less than 20% of its weight is steel. Inside, the amount of technology needed to fly aircraft continues to increase. All of this technology needs to be interconnected using copper-based cabling, terminated with high-grade connectors.
Leveraging Lightweight Interconnects and Cables
Many aircraft manufacturers are now turning to optical interconnect to reduce the amount of copper cable used and the size, space and weight needed for the complex wiring looms. The development of higher density connectors that replace metal casings with plastic housings is also geared towards reducing the overall weight of interconnections.
Around 10% of the electrical signal connections in an aircraft use coaxial cable. The F-35 combat aircraft has around 1.5 miles of coaxial cable, while the B-1B bomber has as much as 15 miles of coaxial cabling. In terms of weight reduction, even a small percentage would equate to a significant total weight.
It would be difficult to reduce the density of the copper used in the core of coaxial cable, however developments in applying metal over polymer filaments has led to new conductive fibers that can be used in place of solid metals. These conductive fibers can be braided using conventional techniques to produce an outer screen layer for coaxial cables that is lighter and stronger than metal.
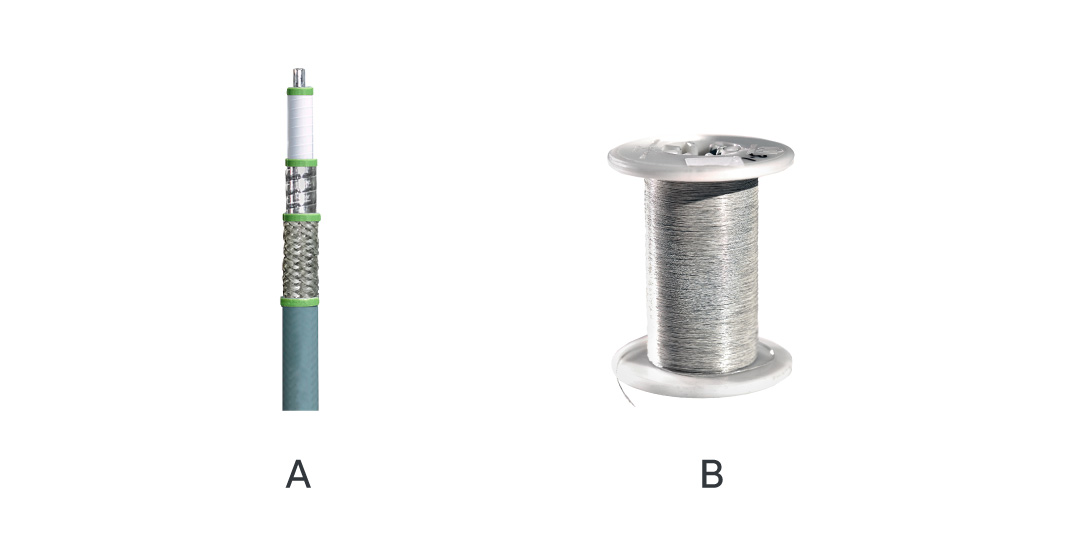
Figure 1: a. Example of a coaxial cable using a braided carbon fiber for the outer screen layer. The carbon fiber is lighter and stronger than conventional materials. b. A spool of carbon fiber used to create the metalized fiber in the cable.
Metalized Fiber Shielding in Practice
Most coaxial cable features a core conductor housed in a dielectric material and surrounded by at least one layer of shielding. In some demanding applications electromagnetic interference and susceptibility need to be further minimized. Here, there will be a second outer shield. Using metalized fiber for the outer shield can reduce the weight of the wire used for this layer by at least 30% and as much as 70% when compared against a shield fabricated using 30 AWG copper.
The material is constructed by depositing silver particles onto a fiber, which can then be processed like regular copper. The tensile strength of a single strand of copper is extremely low, being no stronger than human hair. Metalized fiber, however, has a much higher tensile strength while still being lighter overall. This means it can be processed in a braiding machine in just the same was as copper, to create the outer shield. Terminating the metalized fiber is slightly more complex than using regular copper, which is why Cinch is planning on delivering this innovative material as part of its cable assembly product offering.
Strength and Weight Advantages
Saving weight is significant in any application, but in aerospace it can be even more impactful. For a cable with an average length of around 24in, the weight reduction gained from using metalized fiber could be as much as 20%. When this is considered in terms of the many miles of coaxial cable needed in most aircraft, the weight reduction would be measurable in both financial and environmental terms.
As well as being lighter, the metalized fiber is stronger than standard copper wire, with as much as five times greater break strength. This could be particularly important in military applications, where stresses might be higher than in commercial aircraft. The way Cinch proposes to utilize this material is in cable assemblies and it is now actively developing new connector solutions that can be used with the metalized fiber.
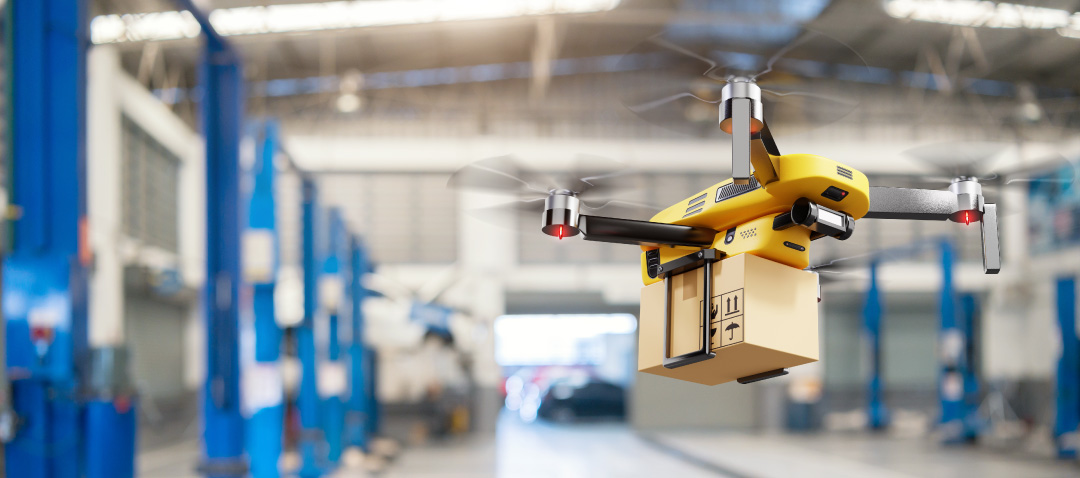
Figure 2: Drone delivering package.
Applications for Metalized Fiber
The metalized fiber material meets NASA outgassing requirements of 1% TML (Total Mass Loss) and 0.1% CVCM (Collected Volatile Condensable Materials) as tested per ASTM E595, meaning it can also be used in space applications. This is perhaps even more significant than its potential use in aviation because the cost of putting anything into space is considerably higher than putting it into the air. As more commercial companies introduce services designed for space tourism, the need to optimize for cost becomes even more acute.
Of course, it isn’t just people that are taking to the air. The use of drones is increasing, and they are now being trialled as final mile delivery solutions. Delivery drones take small packages and transport them direct to the customer. Again, the navigation systems on these small autonomous devices are complex and use multiple types of sensors, including image sensors and camaras. There is a clear advantage here to reducing the weight of the vehicle, as it allows more weight to be attributed to the payload. In this application, even a few ounces can make a big difference. Using metalized fiber coaxial cables here could provide that extra margin.
Industrial automation can also take advantage of the increased robustness offered by metalized fiber. It offers higher levels of flexibility than its copper equivalent, meaning it is more suitable in applications that require repetitive movements. Industrialized robots fit this profile and also meet the need for high-speed signal routing.
Autonomous Mobile Robots (AMRs) is another area where technology is defining a new generation of solutions. AMRs are designed to assist in the workplace or industrial environment. As they can move independently, they rely on sensor clusters to inform them of their location and surroundings. Again, image sensors will be critical here and the use of high-definition, high bandwidth signals will be essential. Electrically operated with an onboard power source, the operational weight of these devices will be important from several aspects. Their uptime will be closely related to their overall weight, but from a safety aspect, manufacturers will be keen to keep their overall mass as small as possible. Using a weight-optimized connectivity solution like metalized fiber coaxial cable could help in this respect.
There is also an opportunity presented by the move towards electrification and the automation of road vehicles. Today, ADAS augment the driver’s actions to control the vehicle, often the connection here is visual. While technologies such as radar and lidar are already being used in ADAS, the use of video will continue to be important going forward. That may mean the driver is presented with visual information, such as the perimeter of the vehicle while parking. Increasingly, the vehicle itself will access this information. This may be, for example, to identify a road traffic sign showing a change in speed restrictions. The trend here is for higher resolution video signals using HD formats. This is increasing the density of high-speed video signals around an already complex wiring system. The wiring loom in a modern vehicle is now often the second heaviest component, after the engine itself. Reducing the weight of additional cabling through the use of metalized fiber in coaxial cables could prove valuable.
Clearly not all applications will require the light-weight strength offered by metalized fiber, but for those where total mass and durability are essential, it will provide a valuable alternative to copper braided shielding. This will include an increasing number of applications going forward, thanks to the increasing demand for higher bandwidth in challenging applications.
Other Weight-Saving Developments for Powered Flight
As well as using metalized fiber to replace copper in coaxial outer shielding layers, Cinch is working on several other technologies that can deliver higher performance with lower weight.
These include using optical interconnect instead of copper. In terms of weight, optical fiber delivers much more bandwidth for the same mass. New technologies like expanded beam connectors are making optical fiber even easier to use in more verticals, including military and aerospace, industrial and even explosive environments.
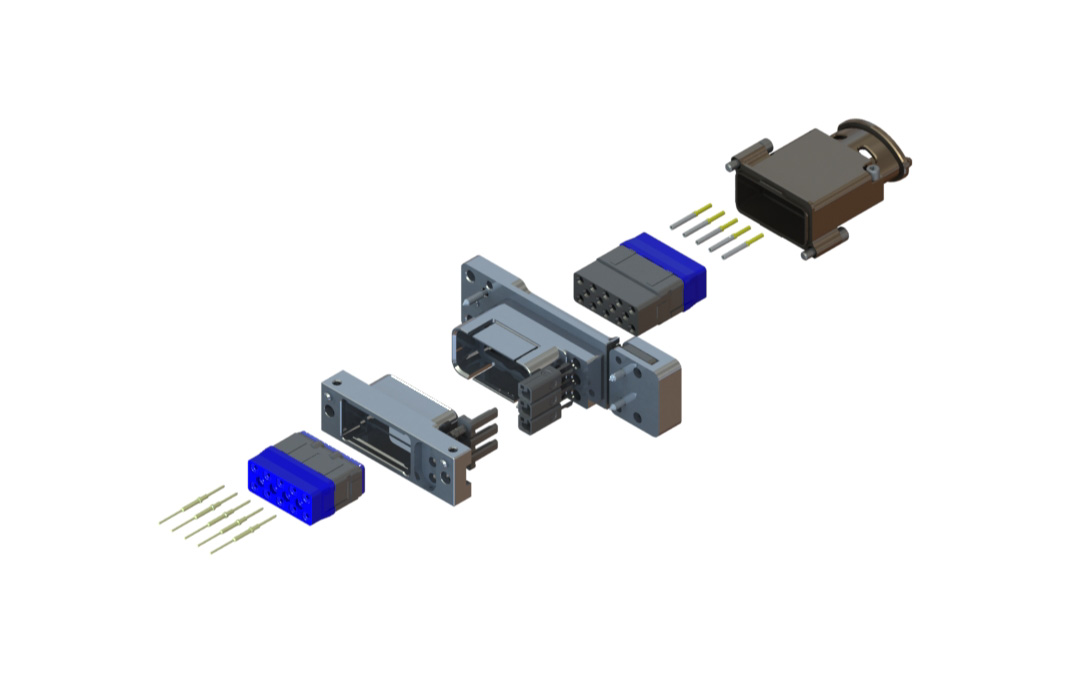
Figure 3: The C-ENX range of modular connectors.
Electrical interconnect is still the most pervasive technology and, here, the standards ARINC 809 and EN4165 are synonymous with the commercial aerospace industry. Solutions like the C-DMX™ (Durable, Module, eXchangable) and C-ENX™ from Cinch have been designed to provide just that, comprising the plug and socket shell, inserts, contacts, backshell and accessories.