While the idea of air taxies and cars that can transform into planes is an old one, till this day it remains nothing more than a concept due to the immense engineering challenge it presents. However, with ongoing advances in power electronics, energy storage technologies, and the obstacles faced in metropolitan areas, the concept of electric vertical take-off and landing aircraft may soon become a reality, with some businesses already having FAA approvals to trial out such systems. What challenges do eVTOLs have to overcome to become practical, how do cables and connectors factor in, and how can Cinch’s range of products help engineers advance this technology?
What Is eVTOL and Why Could It Work?
In today's world, transportation methods cover every environment—land, air, and sea. While these traditional modes have been established for decades, innovative technologies are constantly offering new, sometimes unconventional, alternatives. One such innovation is eVTOL, or electric vertical take-off and landing vehicles. Drawing inspiration from quadcopter drone technology, eVTOLs promise impressive freedom, safety, and automation potential.
As the name implies, eVTOLs are designed to take off and land vertically, eliminating the need for long runways, much like commercial drones. However, unlike drones with fixed upward-facing rotors, many modern eVTOLs are equipped with tilting engines, which allow for forward thrust and improved efficiency in flight.
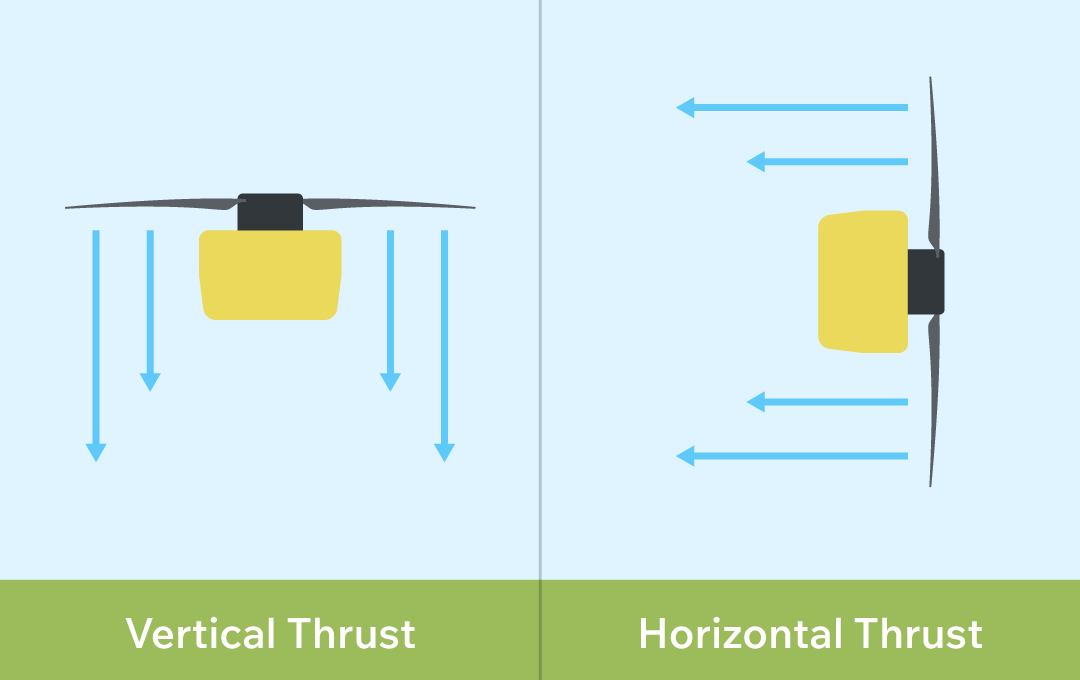
Figure 1: eVTOL engines are designed to tilt and allow both vertical and horizontal thrust.
Compared to helicopters, which are notoriously complex to operate, eVTOLs offer simpler controls, making them easier to pilot. Even more compelling is the possibility of autonomous flight thanks to the robust software and hardware already developed for drones. This could eventually remove the need for pilots altogether.
In terms of airspace, eVTOLs would have a clear advantage in urban areas, where the air above is unused. These vehicles could navigate quickly, drastically cutting down travel times within cities. They also have the potential to reduce congestion by ferrying passengers and cargo, easing the load on ground transportation systems.
While increasing road and rail capacity typically requires expensive infrastructure like tunnels or bridges, eVTOLs would only require landing pads and charging stations. This reduces both the financial burden on taxpayers and the wear and tear on roads, which could lead to lower maintenance costs if more people opt for air travel in urban areas.
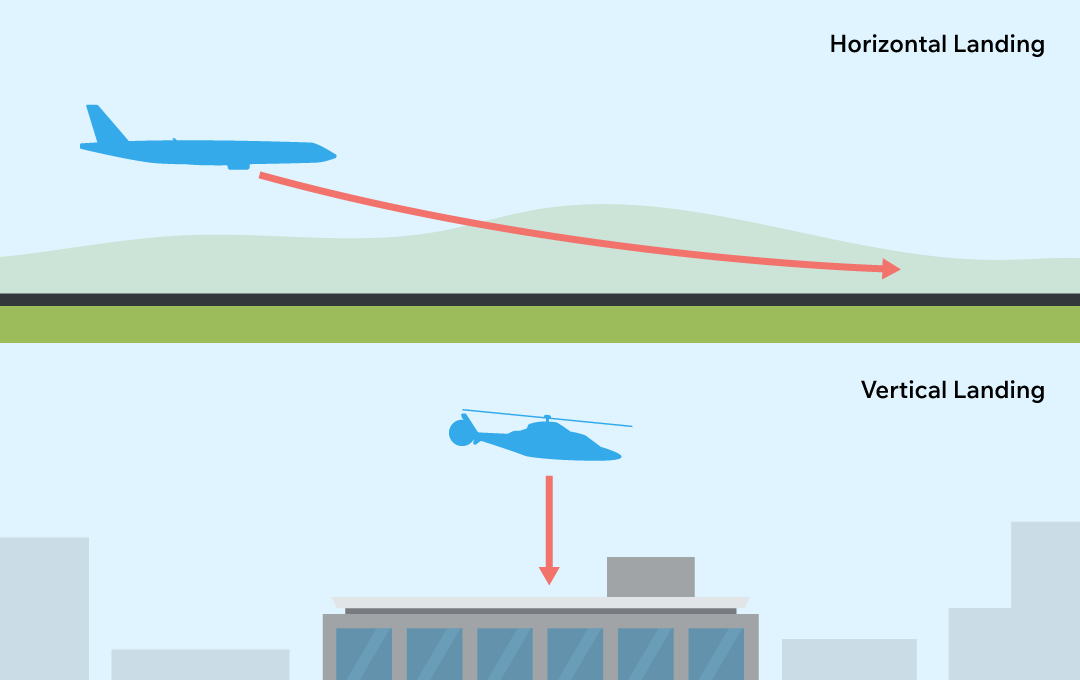
Figure 2: Vertical take-off and landing (top) require much more space than vertical take-off and landing (bottom).
The Key Challenges Facing eVTOLs?
Despite the numerous advantages eVTOLs offer, they remain more of a concept than a commercially viable solution due to several significant challenges.
One of the most critical issues is their reliance on batteries, which are far heavier than traditional fossil fuels like gasoline or natural gas. The energy density of batteries is much lower—gasoline has an energy density of 47.5 MJ/kg, whereas lithium-ion batteries only offer 0.3 MJ/kg. This means a battery capable of storing the same energy as a gasoline tank would be significantly heavier. Additionally, unlike fuel tanks that lighten as fuel is consumed, a battery’s weight remains constant, further impacting efficiency.
Another challenge is the immense energy required to lift the vehicle vertically, which demands not only high energy storage but also powerful converters and cabling to deliver energy quickly. Planes can take advantage of wings for lift, but eVTOLs must rely solely on battery power.
Several other challenges facing eVTOL technology include:
- Battery Weight: Batteries are heavy, and their weight decreases overall efficiency.
- Energy Density: Batteries have a far lower energy density than fossil fuels, resulting in shorter ranges and more weight.
- Power Infrastructure: Charging stations would need to deliver megawatts of power quickly, creating dangerous installation risks and requiring major upgrades to energy grids.
- Material Costs: To compensate for heavy batteries, lightweight materials like carbon fiber are needed, which increases cost and complexity.
- Environmental Concerns: If eVTOLs are charged using energy from fossil fuels, they may actually be less eco-friendly than conventional aircraft.
- Autonomous Navigation: Communication between eVTOLs will need to be seamless and instantaneous to prevent collisions, requiring 5G networks and advanced computing for real-time data transmission.
- Increased Power Consumption: Autonomous systems, AI, and sensors will add further power demands, reducing the energy available for flight.
How Do Connectors and Cables Affect eVTOL Design?
In the design of eVTOLs, it may seem like cables and connectors play a minor role in performance and feasibility, but they are among the most critical components. Each type of connector plays a crucial role in ensuring efficiency, reliability, and safety across various systems within an eVTOL.
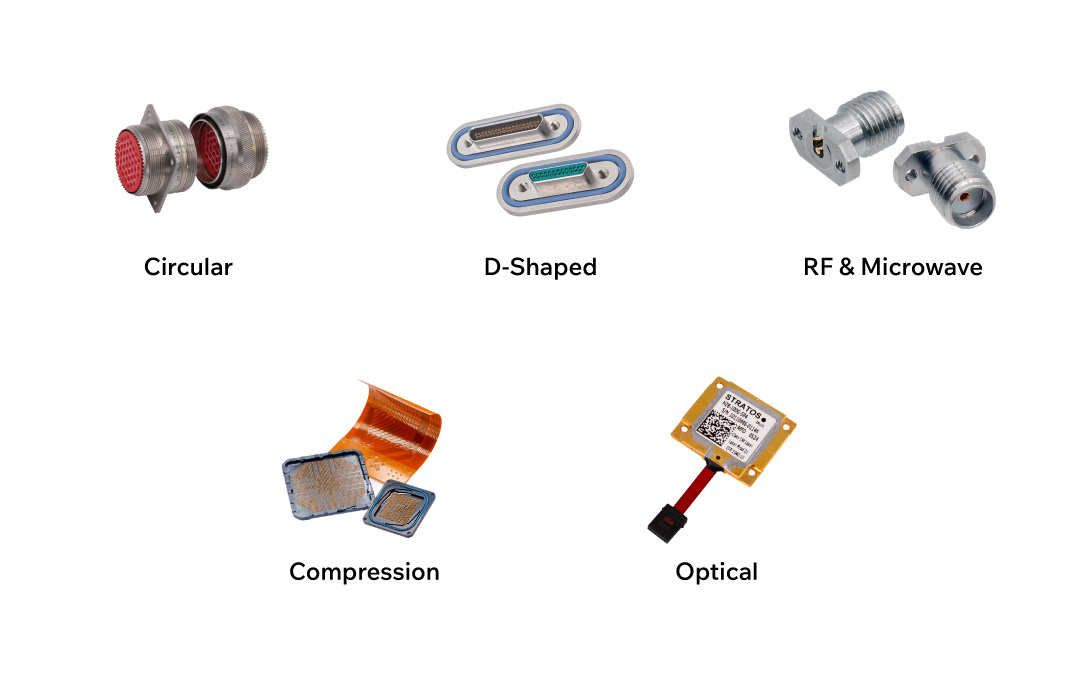
Figure 3: eVTOL have a range of interconnect needs.
Circular Connectors -
For high-power delivery from batteries to motors, circular connectors are ideal. These connectors can handle the high voltages and currents necessary for eVTOL power systems while maintaining robust insulation for protection. Circular connectors offer high power efficiency, essential for managing the high-voltage, high-current demands in eVTOLs. Additionally, they provide the necessary durability to withstand harsh environmental conditions, such as extreme temperatures and weather, while being light enough to minimize the craft’s overall weight.
D-Shaped Connectors -
D-shaped connectors, such as Cinch’s Dura-Con range, are commonly used in aerospace for sensor systems, and they offer reliability in applications that require numerous mating cycles. In eVTOLs, sensors are vital for navigation, flight control, and autonomous systems, making the choice of D-shaped connectors critical for ensuring accurate, real-time data transmission. These connectors provide secure, high-quality connections that resist shock and vibration, making them perfect for the rigorous demands of eVTOL operations.
RF & Microwave Connectors -
eVTOLs rely on various RF systems for communication, navigation, and sensor data transmission. RF & Microwave connectors are essential for handling high-frequency signals, such as those needed for 5G communication and mmWave technologies. These connectors ensure low-latency, high-speed data transfer, which is critical for autonomous flight systems and collision avoidance. With the increasing use of AI and advanced sensing, RF connectors provide the necessary shielding to maintain signal integrity over long distances and under challenging conditions.
Compression Connectors -
Compression connectors play a key role in ensuring high power efficiency and reliability in quick-charging systems. These connectors are designed to handle the extreme voltages, currents, and environmental stresses encountered during rapid charging of eVTOL batteries. They are engineered to endure frequent mating cycles, resist corrosion, and provide secure connections in both high-temperature and high-moisture environments, ensuring that eVTOLs can charge quickly and safely.
Optical Technology -
Optical connectors are vital for high-speed data transmission in eVTOLs, particularly for AI systems, autonomous controls, and real-time sensor networks. Optical connectors provide low-latency, high-bandwidth communication that supports the vast data requirements of eVTOLs, ensuring that data from sensors and control systems are transmitted with minimal interference. Furthermore, optical technology is lightweight, making it ideal for reducing the overall weight of the craft while maintaining strong data connections, even in the presence of electromagnetic interference.
Incorporating these advanced connector solutions not only ensures reliable performance in demanding environments but also helps to address challenges like weight reduction, high power efficiency, and communication integrity. Each type of connector plays a unique and pivotal role in making eVTOLs a feasible and efficient transportation solution for the future.
How Can Cinch Help Power the Future of eVTOLs?
Cinch has a long history of designing connectors and cable assemblies for the most demanding environments, including space exploration, defense applications, and other harsh conditions where reliability and durability are critical. These industries require components that can withstand extreme temperatures, vibrations, and exposure to the elements, all while maintaining consistent performance. Cinch’s expertise in these areas has enabled engineers to develop innovative technologies, and this same experience positions us as a leader in supporting the development of eVTOL systems.
As eVTOL technology evolves, it will face similar challenges to those found in aerospace and defense—where safety, precision, and resilience are non-negotiable. From power distribution to data connectivity, Cinch’s connectors and cable assemblies are designed to endure the rigors of high-power systems and complex data environments. Our experience in creating solutions for the harshest environments ensures that we are well-equipped to help engineers overcome the unique challenges of eVTOLs, paving the way for a new era of urban transportation.